Tapioca starch production process
Here is the tapioca starch production process flow:
Belt conveyor → Spiral cleaning machine → Paddle washing machine → Cassava cutting machine → Cassava starch extrusion crushing machine → Starch filtering machine → fine filtering machine → Sand remover → Starch refining system → Starch dehydrating machine → Starch drying and packing machine
Cassava & cassava starch
The following is the detail introduction of tapioca starch production process
1. Selection of raw material: The quality of starch has a great relationship with the selected raw materials for tapioca starch production process. The cassava yield of less than 10 months is low. The old cassava has been woody for more than 24 months, causing great difficulties for crushing. The increase in the rate of cost reduction will affect the economic benefits. The first step is to ensure that the raw materials are put into storage.
2. Cleaning and washing: Cassava Coarsely cleaning of potatoes takes place during the transport of potatoes to the scrubber by channel for tapioca starch production process. The main cleaning is conducted in dry sieve. The stones, sludge and light wastes are removed at this step. Then the cassava is transported into paddle washing machine for removing the remaining sand, dirt, soil and other debris. Water used for washing is then purified and recycled back into the process.
3.Cassava cutting and crushing: Due to the cassava root is very long and the part near the steam is already woody, it is difficult to crushing it directly without cutting for tapioca starch production process. The quality of crushing will directly affect the output of starch and the next process. Generally, the diameter of the cassava piece is 1cm.Then the cassava piece enters into rasper where the cassava is crushed into slurry so as to release free starch from the cell of cassava roots.
Cassava washing machine
4.Starch filtering: After rasping, the starch slurry enters into the centrifuge sieve where the fiber and starch slurry are separated for tapioca starch production process. Centrifugal screen uses centrifugal force to complete the filtering process and achieve separation of starch slurry and residue which plays a certain role in the yield of starch. At a later stage, the fiber is further separated by fine fiber sieve so that the quality of final starch ca be ensured.
5.Sand remover: In tapioca starch production process, sand is an factor which will influence the taste of final starch, therefore it is important to remove sand out of starch slurry. The starch slurry is transported by the screw pump to the sand removal cyclone to remove the sand grains.
6.Starch refining system: The starch milk enters a 24-stage concentrated cyclone scrubbing unit for tapioca starch production process where the process water is pumped from the other end of the cyclone station to wash the starch in a countercurrent manner. The whole cyclone station can be divided into three parts. First, the starch milk is dehydrated and concentrated by a concentrated cyclone station, and the concentrated starch milk enters the latter 18-stage washing unit, and the cell liquid from the overflow enters the recycling cyclone station. The starch contained therein is recovered. The starch milk from the cyclone station is pumped into a stainless steel starch milk storage tank with a stirrer.
Cassava starch refining machine
7.Starch dehydrating: The concentrated starch milk still contains much water which should be dried after further dehydration. Peeler centrifuge is used for this purpose for tapioca starch production process. After dehydrating, the water content is less than 40%. And siphon peeler centrifuge can decrease water content to 36.5%.
8. Starch drying and packing: The dehydrated starch cake is conveyed to the flash dryer through a conveyor belt for drying for tapioca starch production process. The clean air heated by the heat exchanger is sent to the drying tower to be mixed with wet starch. The water is vaporized in 2-3 seconds and discharged through a separator. Then the fine starch is transferred to a starch silo for temporary storage and cooling. After that, it is transported to a semi-automatic packaging machine and packaged into finished products of 25 kg or 50 kg.
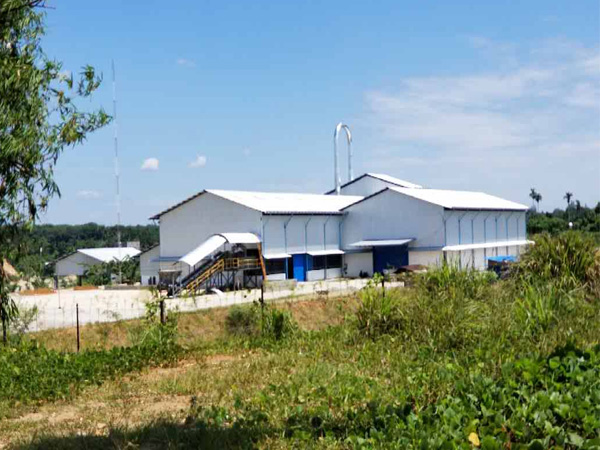
-
Cel/WhatsApp: +8613526615783
-
Phone: +86 371 5677 1822
-
E-mail: market@doingmachinery.com
-
Address: Room 1408,14th Floor,Building 9,No.133 Yaozhai Road,Jinshui District,Zhengzhou City,Henan Province,China